Choosing the Right **China Nylon Mold Manufacturer** for Your Business
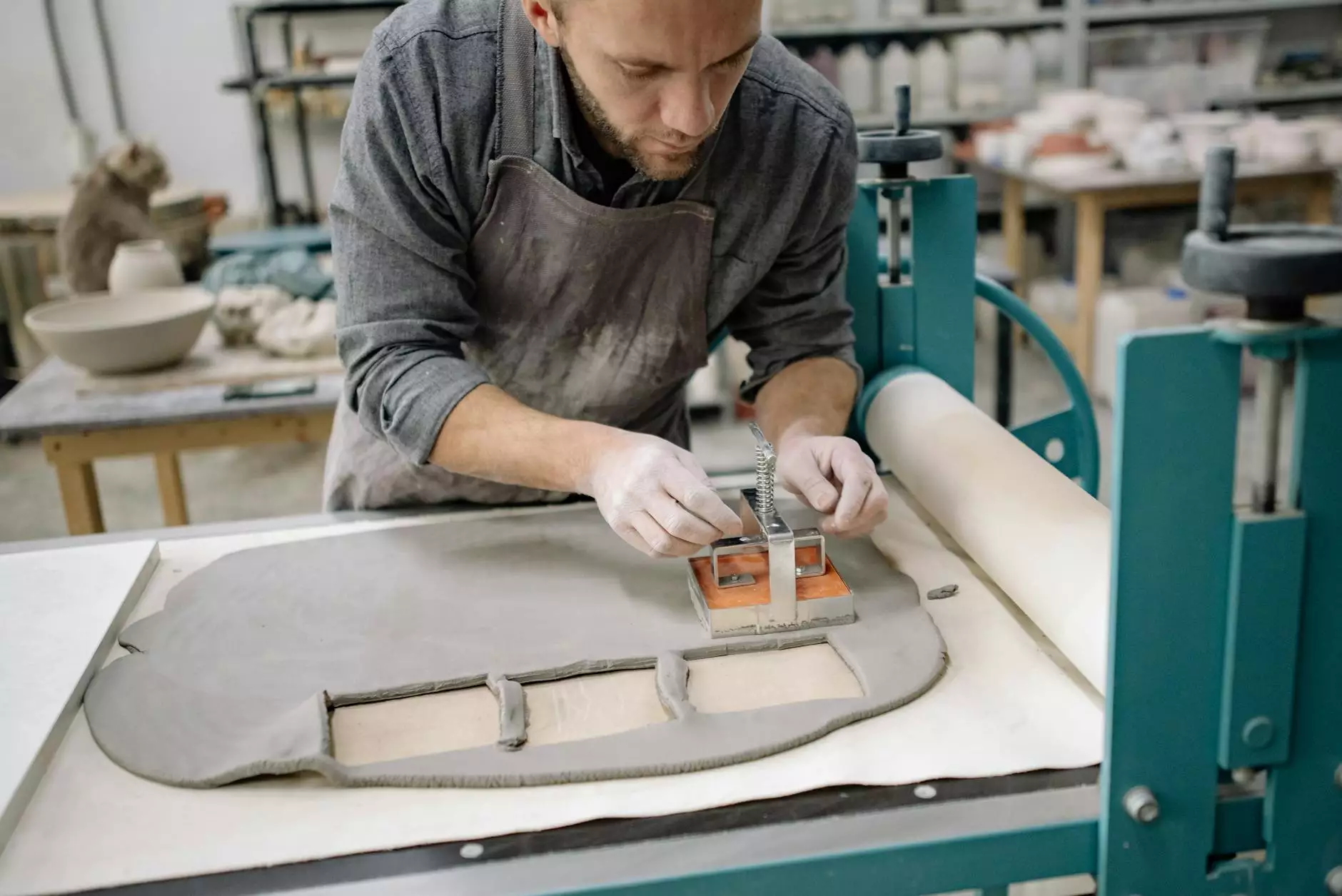
In today’s rapidly evolving manufacturing landscape, partnering with the right China nylon mold manufacturer can significantly enhance the productivity and quality of your products. Nylon molds are essential in various industries due to their durability, flexibility, and resistance to wear and tear. In this article, we delve into the intricacies of plastic mold making and why choosing a reputable manufacturer is imperative for your business success.
The Growing Importance of Molding in Manufacturing
Manufacturing efficiency is often tied directly to the quality of plastic molds used in production. Molding contributes significantly to the overall cost-effectiveness of product development, especially in industries such as automotive, consumer electronics, and packaging. As products increase in complexity, the need for precision-made molds becomes more crucial.
Why Choose a China Nylon Mold Manufacturer?
China has established itself as a global leader in manufacturing, offering unique advantages that appeal to businesses worldwide:
- Cost-Effectiveness: Manufacturers in China often provide competitive pricing, allowing businesses to reduce their production costs significantly.
- Advanced Technology: Many Chinese mold manufacturers invest in state-of-the-art technology, providing high precision molds that meet international standards.
- Experienced Workforce: The workforce in China has vast experience in mold making, contributing to superior quality products.
- Scalability: Chinese manufacturers can handle large scale production, ensuring that you can meet industry demands without compromising on quality.
Understanding Plastic Molding Techniques
There are several plastic molding techniques employed in the industry; understanding these can help you choose the right manufacturer and technique for your project:
1. Injection Molding
Injection molding is the most commonly used method for producing parts from both thermoplastic and thermosetting plastic materials. This technique involves injecting molten plastic into a mold, where it cools and hardens into the desired shape. This process is ideal for producing large volumes of the same part, making it economically viable.
2. Blow Molding
This method is predominantly used for creating hollow objects, such as bottles. In blow molding, air pressure is used to inflate heated plastic inside a mold, forming the desired shape.
3. Compression Molding
Compression molding involves placing a heated polymer into a mold cavity, which is then closed, allowing the material to flow and cure. It is commonly used for rubber and thermosetting plastics.
Key Attributes of a Reliable Plastic Injection Mould Manufacturer
When selecting a plastic injection mould manufacturer, several factors are essential to ensure you partner with a reliable company:
1. Quality Assurance
The manufacturer should have strict quality control protocols in place. Look for certifications such as ISO 9001, as they demonstrate a commitment to quality management.
2. Range of Services
Choose a manufacturer that offers a comprehensive range of services, including design assistance, prototyping, and ongoing support after production.
3. Communication
Effective communication is key to any successful business partnership. Ensure that the manufacturer can provide support in your preferred language and is responsive to inquiries.
4. Lead Times
Reliable manufacturers will provide realistic lead times and adhere to them, helping you meet your project deadlines.
The Process of Working with a Manufacturer
Once you’ve selected a China nylon mold manufacturer, the process typically involves several key steps:
1. Design Consultation
The manufacturer will often work with your design team to understand your specific needs and make necessary adjustments to the mold design for manufacturability.
2. Prototyping
Creating a prototype allows you to test the design and functionality of your mold before mass production begins, reducing the risk of costly errors later.
3. Production
Upon approval, the manufacturer will commence production, strictly following the agreed-upon timelines.
4. Quality Checks
Throughout the production process, continuous quality checks ensure that the molds produced meet the required specifications and standards.
Future Trends in Plastic Mold Manufacturing
As technology continues to evolve, several trends are shaping the future of plastic mold manufacturing:
1. Automation and Robotics
Manufacturers are increasingly turning to automation and robotics to improve efficiency, reduce human error, and lower labor costs.
2. 3D Printing Integration
The integration of 3D printing in mold-making processes allows manufacturers to create complex designs faster and at lower costs, revolutionizing the industry.
3. Sustainable Practices
With an increasing focus on sustainability, manufacturers are adopting eco-friendly practices, from reducing waste in the production process to using recyclable materials.
Conclusion
Choosing the right China nylon mold manufacturer is a strategic decision that can greatly impact your production quality and cost. By considering factors such as technology, quality assurance, and communication, you can select a partner that aligns with your business objectives. Moreover, understanding the various molding techniques and emerging trends can position your company for future growth and innovation. Investing in high-quality nylon molds from a reputable manufacturer like Hanking Mould can lead to better products and increased customer satisfaction.
Call to Action
If you're ready to take the next step in enhancing your manufacturing capabilities, consider reaching out to Hanking Mould, a leading plastic injection mould manufacturer. Our expertise in nylon molds ensures you receive the best products tailored to your specific needs.