Buy Plastic Injection Molding: A Comprehensive Guide for Metal Fabricators
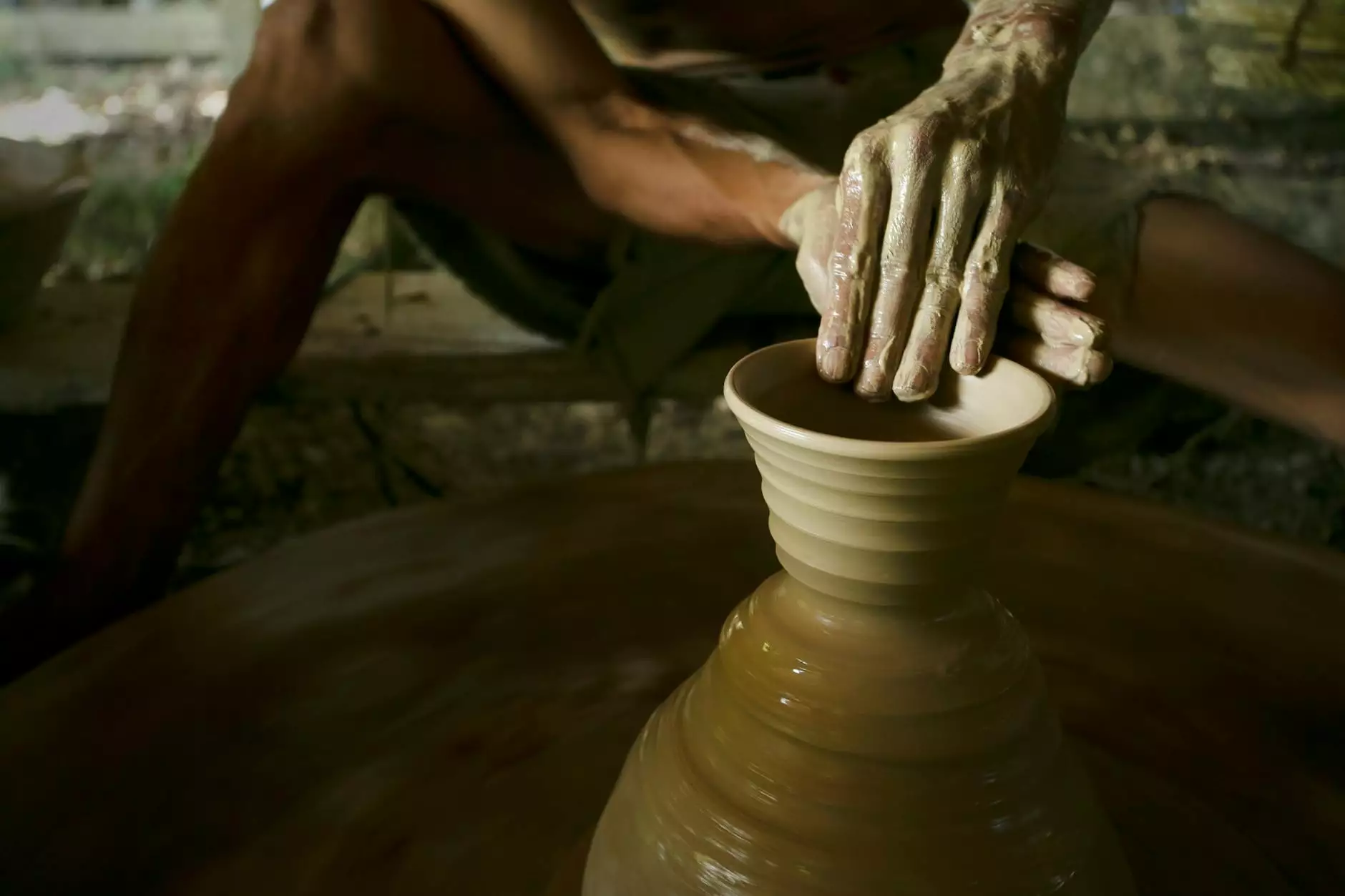
In the rapidly evolving manufacturing landscape, buying plastic injection molding has become a pivotal decision for many businesses aiming to enhance their production capabilities. This article explores the essential aspects of plastic injection molding, its advantages, and why partnering with experienced metal fabricators can lead to unprecedented efficiency and quality in your production line.
Understanding Plastic Injection Molding
Plastic injection molding is a manufacturing process that involves injecting molten plastic material into a mold to create high-precision plastic parts. This process offers a myriad of benefits, making it one of the most widely utilized methods in the production of plastic components across diverse industries.
Key Advantages of Plastic Injection Molding
- High Efficiency: With the ability to produce thousands of parts in a single cycle, it's an ideal choice for mass production.
- Cost-Effectiveness: While the initial investment in molds can be high, the per-unit cost decreases significantly with larger production runs.
- Design Flexibility: Complex shapes can be easily attained, allowing for innovative designs that meet specific customer needs.
- Material Variety: A wide range of thermoplastics and thermosetting plastics can be utilized, enhancing the versatility of the final products.
- Minimal Waste: The process generates minimal waste compared to other manufacturing methods since excess material can be reused.
How to Buy Plastic Injection Molding Services
When considering to buy plastic injection molding services, several critical steps should guide your decision-making process:
1. Identify Your Needs
Before approaching a metal fabricator, it's essential to clearly define your project requirements. Consider the following:
- What type of plastic materials do you need?
- What is the volume of parts required?
- What specifications must be met (dimensions, tolerances, etc.)?
- What level of detail is needed in the mold design?
2. Research Potential Metal Fabricators
Finding the right partner is crucial. Research potential metal fabricators like DeepMould.net, who specialize in plastic injection molding. Look for the following:
- Experience in your specific industry.
- Portfolio of past projects and client testimonials.
- Technological capabilities and services offered.
- Customer support and communication strategies.
3. Request Quotes and Consultations
Once you’ve pinpointed a few potential fabricators, reach out to them for quotes. Provide them with your requirements and ask for detailed proposals. Consider factors like:
- Pricing breakdowns and payment terms.
- Lead times and production schedules.
- Post-production services such as quality control and logistics.
4. Evaluate Prototypes
Before committing to full-scale production, it’s wise to evaluate prototypes or sample parts. This allows you to assess the quality and ensure that the specifications are met adequately.
The Process of Plastic Injection Molding
1. Material Preparation
The process begins with preparing the plastic material. The raw plastic pellets are fed into a hopper, which then moves to a heated barrel where they are melted.
2. Injection
Once the plastic is molten, it is injected into a mold under high pressure. The speed and force of injection are controlled to ensure consistency and accuracy.
3. Cooling and Solidification
After injection, the mold is cooled, and the plastic solidifies into the desired shape.
4. Ejection
The mold opens and ejects the finished part, ready for any post-processing or assembly that might be required.
Post-Processing Techniques in Plastic Injection Molding
Even after the molding process is complete, additional finishing techniques can enhance the final product, such as:
- Surface Finishing: Techniques like sanding, polishing, or painting to improve aesthetics.
- Assembly: Combining multiple molded parts into a final product.
- Quality Control: Implementing rigorous testing and inspections to ensure the parts meet all specifications.
Choosing the Right Materials for Injection Molding
The choice of material in plastic injection molding can greatly influence the properties of the final product. Some common materials include:
- ABS (Acrylonitrile Butadiene Styrene): Known for its toughness and impact resistance.
- PP (Polypropylene): Light and flexible, offering excellent chemical resistance.
- PVC (Polyvinyl Chloride): Versatile and cost-effective, often used in various applications.
- PA (Polyamide or Nylon): Strong and durable, ideal for high-stress applications.
The Future of Plastic Injection Molding
As technology advances, the field of plastic injection molding continues to transform. Innovations such as:
- 3D Printing Technologies: Allowing for rapid prototyping and mold creation.
- Smart Manufacturing: Incorporating IoT for real-time monitoring and efficiency improvement.
- Sustainable Practices: Increasing focus on using recycled materials and minimizing environmental impact.
Conclusion
In conclusion, the decision to buy plastic injection molding is a strategic move that can significantly benefit your production needs. By thoroughly understanding the process, advantages, and material selection, and by partnering with reliable metal fabricators like DeepMould.net, you can elevate your manufacturing capabilities to new heights.
As you embark on this journey, remember that informed decisions lead to successful partnerships and outstanding results. Embrace the opportunities that come with plastic injection molding today!