Understanding the Low Pressure Casting Process: A Comprehensive Guide
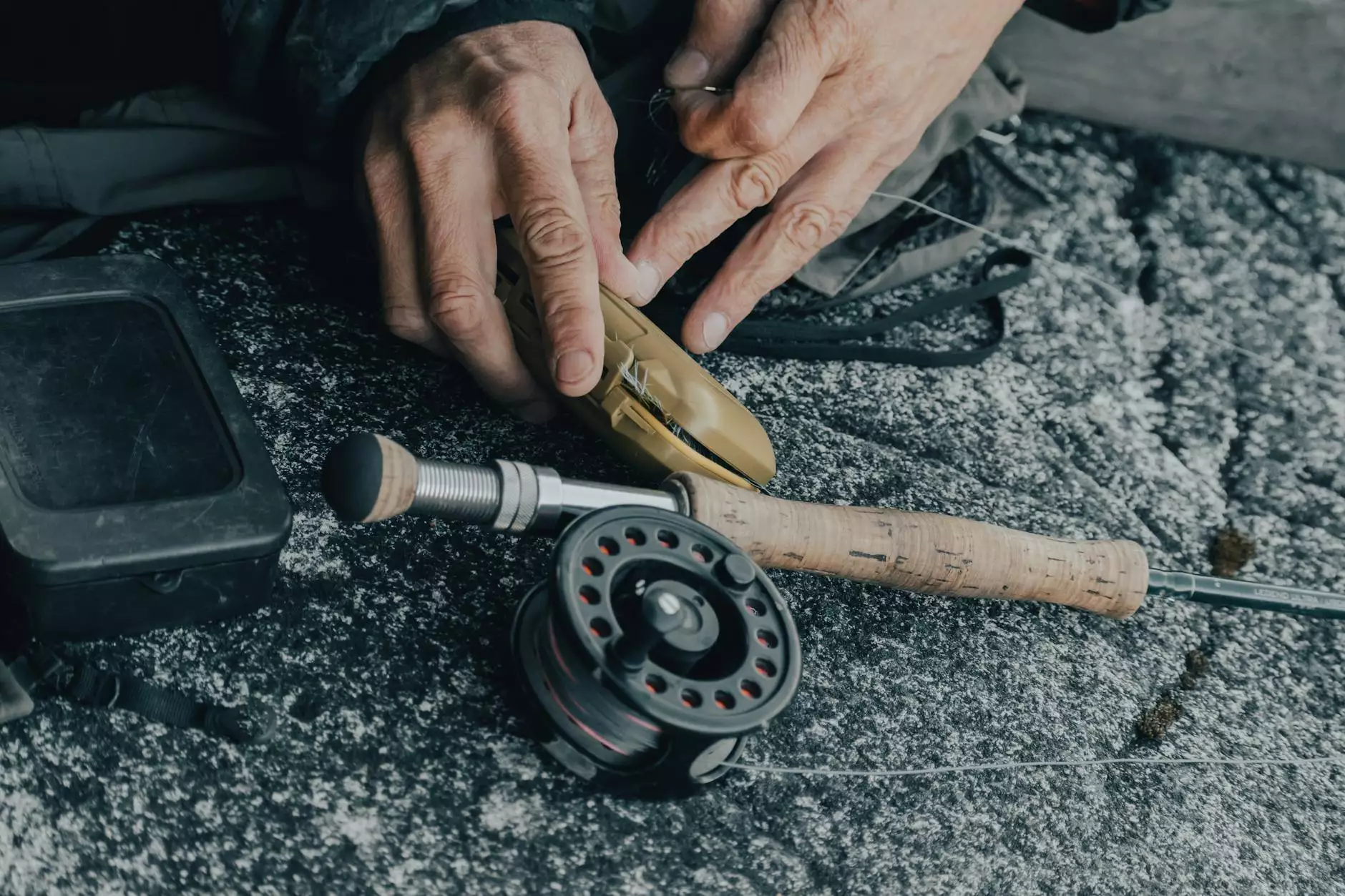
The low pressure casting process is an advanced manufacturing technique that is revolutionizing the way businesses, especially in sectors like Art Supplies, Product Design, and 3D Printing, approach the creation of complex components. In this article, we will explore the mechanisms behind low pressure casting, its advantages, applications, and how it stands out in the competitive manufacturing landscape.
What is Low Pressure Casting?
The low pressure casting process involves the use of a controlled environment to pour molten metal into a mold under low pressure. This method differs from traditional casting techniques, which often rely on gravity and can introduce air bubbles and other imperfections. By employing pressurized gas to push the molten material into the mold, manufacturers can achieve greater accuracy, consistency, and strength in their products.
How Does the Low Pressure Casting Process Work?
At its core, the low pressure casting process can be broken down into several key steps:
- Molten Metal Preparation: The metal is melted in a furnace until it reaches a liquid state. The temperature and composition must be carefully controlled to ensure quality.
- Mold Design: Molds are designed to accommodate the flow of molten metal while minimizing defects. Materials used for molds can vary based on the type of metal being cast.
- Injection of Molten Metal: Using a controlled low-pressure system, the molten metal is injected into the mold. This pressure can range from 0.1 to 1 bar, allowing for enhanced filling and reduced inclusions.
- Cooling and Solidification: Once filled, the metal is allowed to cool and solidify; this is where the final shape and integrity of the product is achieved.
- Mold Removal and Finishing: After solidification, the mold is removed, and finishing processes such as trimming, machining, or surface treatment can enhance the product's appearance and functionality.
Advantages of Low Pressure Casting
The advantages of the low pressure casting process are numerous, making it a preferred choice for various manufacturers:
- High Quality and Precision: Low pressure casting is known for producing parts with tighter tolerances and superior surface finishes.
- Reduced Defects: The controlled injection reduces common casting defects such as air pockets and inclusions, resulting in a stronger final product.
- Increased Production Efficiency: The method allows for quicker cycle times, making it ideal for high-volume production without compromising quality.
- Material Versatility: This process can be used with a wide range of metals, including aluminum, magnesium, and zinc, broadening its application in multiple industries.
- Cost-Effectiveness: While initial setup costs may be higher, the long-term savings from reduced waste and improved quality can offset these expenses significantly.
Applications of Low Pressure Casting in Various Industries
The low pressure casting process has found applications across various fields:
Art Supplies
In the art supplies industry, the low pressure casting technique is used to create durable and intricate components for tools and equipment. For example, specialized casting processes can produce high-quality paint containers or tool handles that require both functionality and aesthetic appeal.
Product Design
Product designers utilize low pressure casting to create prototypes and end-use products that are both efficient and appealing. The precision of this casting process makes it ideal for automotive parts, consumer electronics, and machinery components where performance and design are critical.
3D Printing
The integration of low pressure casting with 3D printing technology has opened up new avenues for producing complex designs. Using 3D-printed molds, manufacturers can employ low pressure techniques to produce intricate components that were previously impossible to create, thereby enhancing innovation in product development.
The Future of Low Pressure Casting
The low pressure casting process is continuously evolving, with advancements in technology leading to improvements in efficiency and capabilities. Some potential future trends include:
- Automation: Increased automation in the low pressure casting process will likely enhance productivity and reduce labor costs.
- Smart Casting Technologies: The integration of IoT and AI can provide real-time monitoring and adjustments during the casting process, further reducing defects and improving quality.
- Sustainable Practices: As the demand for environmentally-friendly manufacturing grows, innovations in low pressure casting may lead to more sustainable processes and materials.
Conclusion
The low pressure casting process represents a significant advancement in manufacturing technology, offering numerous benefits that are reshaping industries like Art Supplies, Product Design, and 3D Printing. By allowing for greater control over the casting environment and reducing the chances of defects, this process is redefining quality standards. As businesses continue to adopt and refine these techniques, we can expect to see even more innovation and improvement in manufacturing practices.
For businesses looking to enhance their production processes and learn more about the low pressure casting process, partnering with experts in the field or incorporating modern technologies can lead to substantial benefits. Let the power of low pressure casting transform your manufacturing capabilities and unlock new opportunities for growth.