Exploring the Potential of ULTEM in 3D Printing and Engineering
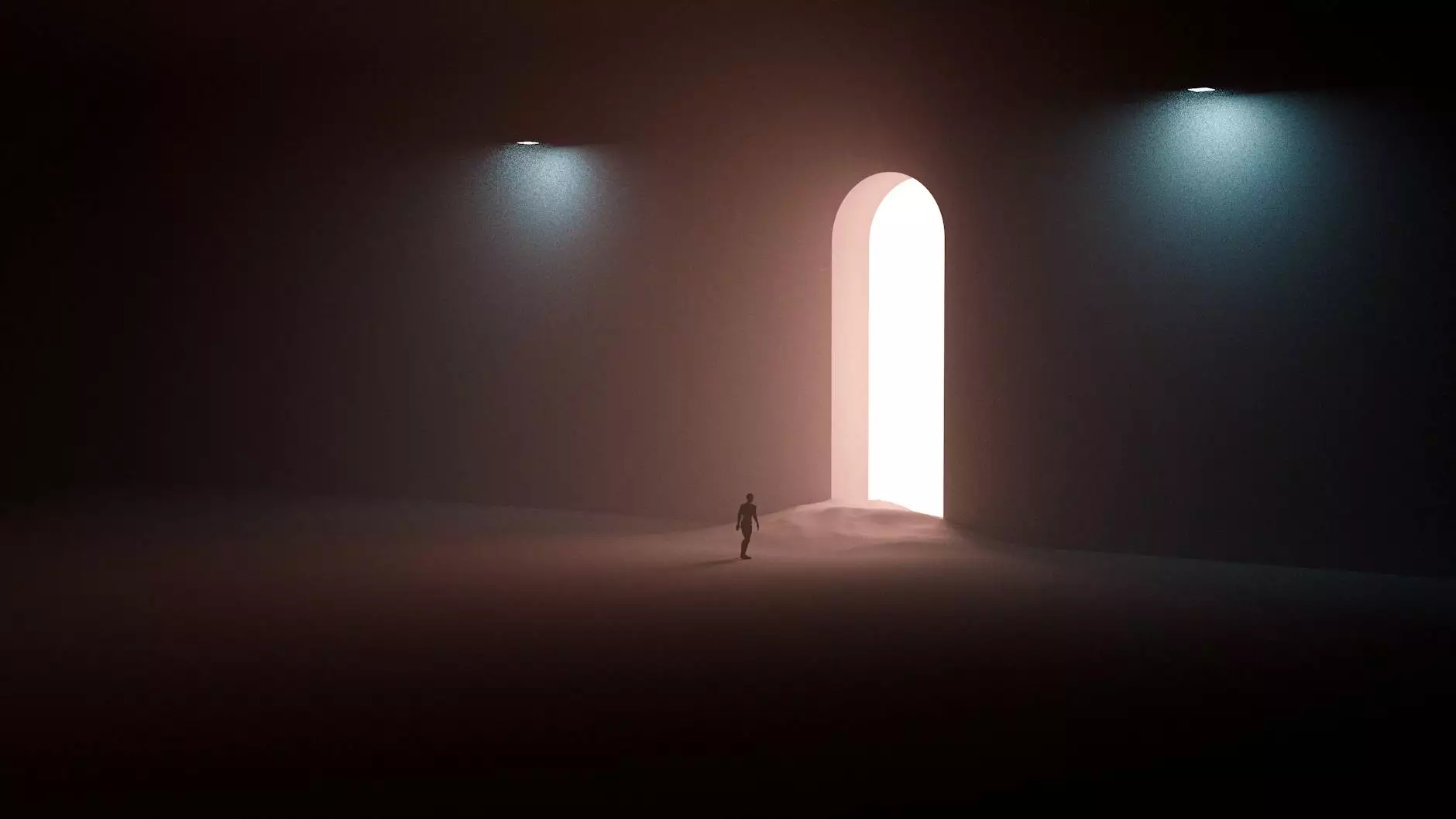
ULTEM, a high-performance thermoplastic polymer, has been revolutionizing the landscape of engineering and manufacturing. Its incredible mechanical properties, thermal resistance, and chemical stability make it a favored choice across various industries that require materials to withstand extreme conditions. In this article, we will delve deeply into the applications of ULTEM in 3D printing, its unique properties, and why businesses should consider integrating this advanced material into their operations.
The Chemistry Behind ULTEM
Developed by GE Plastics, ULTEM is chemically known as polyetherimide (PEI), which is a thermoplastic that combines the benefits of polycarbonate and polyimide. This unique compound features a combination of high strength, rigidity, and dimensional stability, which enables it to perform exceptionally well under stress and heat.
Key Characteristics of ULTEM
- High Heat Resistance: With a heat deflection temperature around 217°C, ULTEM stands out in applications where thermal stability is critical.
- Excellent Mechanical Strength: Displaying outstanding tensile and compressive strength, ULTEM is suitable for heavy-duty applications.
- Chemical Resistance: This material shows resilience against numerous chemicals, making it ideal for rigorous environments.
- Lightweight: The low density of ULTEM ensures that products made from it are both strong and lightweight.
- Flame Retardant: ULTEM has a UL94 V-0 flame rating, thus making it safer for applications requiring fire resistance.
Applications of ULTEM in 3D Printing
The additive manufacturing or 3D printing realm has been remarkably transformed by the introduction of ULTEM. Various industries have been leveraging the unique properties of this material to achieve superior results that are otherwise unattainable with traditional materials. Here are some key applications:
Aerospace Industry
The aerospace sector demands materials that can endure severe conditions while maintaining safety and performance. ULTEM is commonly used to manufacture:
- Lightweight structural components
- Functional prototypes
- Complex geometries that reduce weight without compromising strength
Its flame resistance and thermal stability make it a top choice for components subjected to high temperatures and pressures.
Medical Devices
In the medical field, ULTEM is making waves due to its biocompatibility and sterilization capability. It is used in:
- Surgical instruments
- Wearable health monitors
- Various drug delivery systems
These applications benefit from the material's ability to withstand autoclaving and various sterilization processes, ensuring safe and effective use in healthcare settings.
Automotive Applications
The automotive industry continuously seeks materials that reduce weight while ensuring durability. ULTEM serves as an optimal solution for:
- Interior components
- Functional prototypes for design testing
- Parts that require high strength-to-weight ratios
Its excellent thermal properties are particularly beneficial for automotive electrical components that may operate in high-temperature environments.
Electronics and Electrical Components
With the constant demand for materials that resist heat and electrical currents, ULTEM finds extensive use in:
- Insulators
- Connectors
- Circuit boards
The material’s dielectric properties contribute to its applicability in sensitive electronic components, ensuring safety and efficiency.
Benefits of Using ULTEM in Manufacturing
Incorporating ULTEM into manufacturing processes opens up a world of benefits for businesses. Here are some of the most compelling advantages:
Customization and Design Flexibility
3D printing with ULTEM allows for intricate designs and customization that traditional manufacturing cannot achieve. The ability to create complex shapes reduces material waste and promotes sustainability.
Rapid Prototyping
The speed of production with ULTEM in 3D printing means that prototypes can be developed and tested more efficiently. This rapid prototyping capability streamlines the innovation process, reducing time-to-market and associated costs.
Cost-Effectiveness
While ULTEM may have a higher upfront material cost, its durability and longevity often offset these initial expenses. Products manufactured with ULTEM typically require less maintenance and less frequent replacements.
The Future of ULTEM in Industry
As the landscape of manufacturing and engineering continues to evolve, ULTEM is positioned to play a critical role in future developments:
- Advancements in 3D Printing Technology: Innovations in 3D printing are making ULTEM more accessible and easier to work with, broadening its use across various sectors.
- Sustainable Practices: With a growing emphasis on sustainability in manufacturing, ULTEM’s potential for recycling and reduced waste makes it a favorable option.
- Enhanced Performance Standards: Ongoing research and development are likely to introduce even more efficient variants of ULTEM, maximizing performance and versatility.
Conclusion
In conclusion, ULTEM represents a milestone in high-performance thermoplastics, especially within the field of 3D printing. Its unique properties make it a standout choice for various industries, from aerospace to healthcare and automotive. The continuous evolution of manufacturing technology alongside the inherent benefits of ULTEM indicates a promising future, filled with opportunities for businesses willing to adopt this advanced material.
As businesses like infotron.com.tr explore the vast potential of ULTEM, the landscape of production and design will undoubtedly witness remarkable transformations. Embracing this material is not just about staying competitive—it's about being at the forefront of innovation and excellence.